Jet mills are advanced machines. They use high-speed air or gas jets to grind materials into fine powders. They are widely used in industries like pharmaceuticals and food processing. They can produce ultra-fine powders while keeping low temperatures. A key feature of jet mills is their high powder collection rate. This article looks at the tech that lets jet mills maximize powder collection efficiency.
Thank you for reading this post, don't forget to subscribe!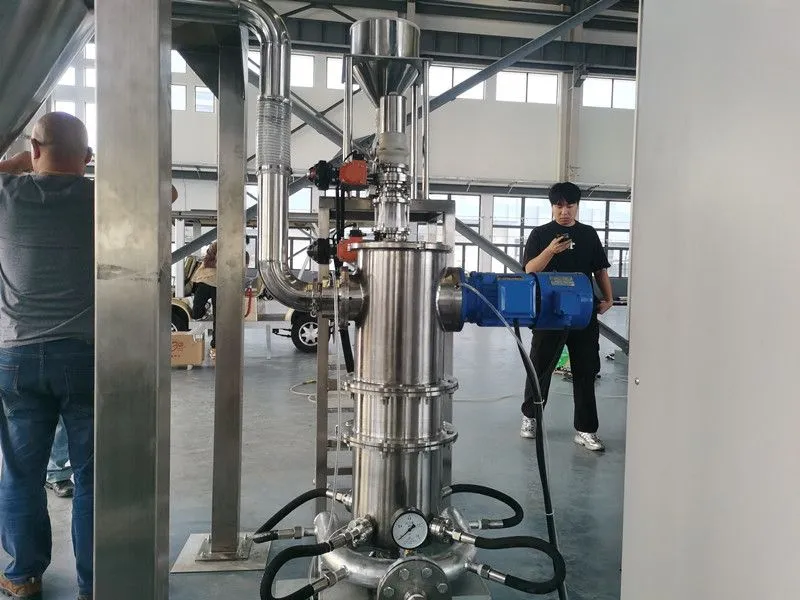
Understanding Jet Milling Technology
Jet milling uses fluid energy. High-pressure air or gas jets accelerate particles. Grinding happens when particles collide at high speeds. This reduces their size. The design of jet mills is critical in achieving effective powder collection rates.
Key Components of Jet Mills
Nozzles: Jet mills usually have multiple nozzles. They direct high-velocity air streams into a grinding chamber. The nozzles’ arrangement and number can affect grinding efficiency and particle size.
Grinding Chamber: The design of the grinding chamber is optimized for turbulence and particle interactions. A well-designed chamber increases particle collisions, leading to better milling.
Cyclone Separators: After grinding, we often use cyclone separators to collect the milled powder. These separators use centrifugal force to separate fine particles from the air stream. This allows for efficient collection.
Mechanisms for High Powder Collection Rates
Achieving high powder collection rates in jet mills involves several interrelated mechanisms:
1. Optimized Airflow Dynamics
Airflow dynamics in a jet mill are crucial. They affect both grinding efficiency and powder collection. High-velocity air jets create turbulence in the grinding chamber, which enhances particle collisions. This turbulence also helps in transporting the milled particles towards the collection system.
Airflow Rate: A higher airflow rate can better remove fine particles from the grinding chamber. This will improve collection rates. But, we must balance airflow with grinding efficiency. This avoids wasting energy.
Pressure Control: Operating at 25 to 100 psig is best. It accelerates particles without damaging the material. Higher pressures can lead to increased particle velocities and improved collection rates.
2. Particle Size Distribution Management
It’s vital to control particle size distribution to maximize powder collection rates. Jet mills can be adjusted to produce specific particle sizes based on application requirements.
Classification Systems: Many jet mills have systems that separate fine particles from larger ones during or after milling. These systems boost yield and quality by collecting only suitably sized particles.
Feed Rate Adjustments: Optimizing the feed rate into the jet mill can affect particle size and collection efficiency. A well-balanced feed rate prevents clogging and excessive wear. It ensures continuous operation.
3. Efficient Collection Systems
The powder collection system’s design is key to high collection rates.
Cyclone Separators: Cyclones separate fine powders from the air stream. They do this based on particle size and density. We can optimize a cyclone’s design parameters for maximum efficiency. This includes its inlet velocity and geometry.
Bag Filters: In some setups, bag filters may work with cyclones. They capture ultrafine particles that may escape during cyclone separation. This dual approach ensures higher overall collection rates.
Factors Influencing Powder Collection Rates
Several factors can affect the efficiency of powder collection in jet mills:
1. Material Properties
The material’s physical properties affect grinding and powder collection rates.
Particle Shape and Density: Irregular or dense particles may flow differently than spherical or lighter ones. Understanding these properties helps in optimizing milling parameters for better collection.
Moisture Content: High-moisture materials may agglomerate during milling. This can reduce collection rates. Pre-drying materials can help mitigate this issue.
2. Operational Parameters
To maintain peak performance, we must control temperature, pressure, and feed rate.
Temperature Control: Jet mills keep low temperatures during operation. But, for sensitive materials that may degrade at higher temps, it’s crucial to monitor temperature changes.
Maintenance Practices: Regularly maintain nozzles and other parts. This ensures consistent performance over time. Clogged or worn-out parts can lead to reduced airflow and lower collection rates.
Applications Benefiting from High Powder Collection Rates
Jet mills with high powder collection capabilities find applications across various industries:
1. Pharmaceuticals
In drug manufacturing, precise control of particle size is vital. It affects the drug’s efficacy. Jet mills can make inhalable powders with high bioavailability. They can achieve fine particle sizes while having high collection rates.
2. Food Processing
Jet milling is a food processing method. It powders ingredients, like spices and flavorings. High collection rates reduce waste in production. This cuts costs and improves product quality.
3. Materials Science
In materials science, jet mills are for making advanced materials, like ceramics and composites. It is vital to have uniform, pure particle sizes. This is key to developing high-performance materials.
Conclusion
Jet mills are a high-tech way to collect powder quickly. They use optimized airflow, effective classifiers, and careful control of settings. Their value lies in their versatility across industries. They produce fine powders to precise specs, with minimal waste and intact products. As technology advances, jet milling processes should improve. This will boost their efficiency and use in various fields.
Manufacturers can improve their use of jet milling tech. They should know the factors that affect its performance. It will help them meet production goals and ensure high quality in all apps.